During the fabulous Pensacon weekend, I ended up in a discussion with members of the SCA (Society for Creative Anachronism – an international organization dedicated to researching and re-creating the arts and skills of pre-17th-century Europe.) As a writer and a medieval era fan, I was intrigued, but my schedule didn’t allow me to attend the major event they had going on. Apparently though, my muses didn’t want to take no for an answer. Another invitation to hang out with the SCA hit me at home only a few weeks later. The local chapter is in the process of revitalizing, my Dungeon Master is a part of that revival, and he really wanted me to come “play.”
As you’re all aware, I’m busy as hedrin, so adding anything to my schedule is a bit of a wrench. Unfortunately for my schedule but fortunately for Billy, he said the word “blacksmithing,” and I was sold. So, for any SCA members that happen by, I’ve been interacting with you guys for only a few weeks, so my lingo might be a bit off. (Please cut me some slack. Please?)
Last Saturday Billy’s son William was taking a blacksmithing class with a smith and unofficial chapter combat marshal Mark (pictured left). To Mark’s surprise, about a half dozen of us showed up to learn. It was for William’s school project, so he got most of the hands on treatment. Me? I’m here mostly for scene and plot information for an upcoming novel (no, I’m not spoiling anything by telling you which one.) Even with William in the center seat the garrulous and generous Mark offered a flood of knowledge that left my head spinning.
We started with a tour of the anvils, including a diagram which I can’t find but may add to this post later. From there he passed around a selection of hammers and tongue, explaining the differences of each, their uses and a dozen other little details – like how the different edges of just one hammer’s face each had a different striking purpose.
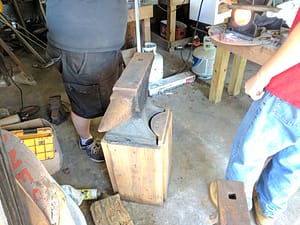
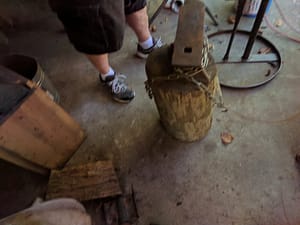




You may be wondering about the other two sides of this rod – I was until Mark explained. The hardened metal plate of the anvil acted as hammer for the under side of the rod.


For the second S-Bend, Mark moved us to a curve maker tool composed of three small, thick metal rings on a plate held in a vice. He simply slid the hot rod between the cast barrels (curly tip as anchor) and bent a perfect curve. Then Mark the Artist took over. The curve maker was removed and the S-Hook positioned in the vice to set it up for the next stage. (Keep in mind this is all being done with gloves, because the rod is still smell-your-flesh-sizzle-like-bacon hot.) One hook was fitted both position and angle, the vice tightened just enough to hold it and the hook went back in the heat. When it came back, Mark tightened it where it belonged in the vice and took a custom forged wrench to the hook and twisted the whole thing around the center – one and a half turns – to create a pretty spiral of cast iron. Showing us (William) how to manage the twist put his hands at a bad angle, so the hook wasn’t quite strait. Mark brought out a hammer which was really just a handle holding a 6-inch long roll of leather and pounded the S-Hook back toward the desired shape. A couple more trips to the forge and some skilled hammer work straightened the S-Hook to Mark’s artistic perfectionist’s delight.
The day was cut short by our impending D&D game – almost everyone there learning is part of the group, but we’ve been invited back to do our own S-Hooks and continue on to advancing our skill enough to make our own cutlery for a feast kit. After we broke up and everyone else was gone, Mark kindly offer me answers and forge time. I’m looking for a gap in the schedule. My characters if not my arm hair are in good hands.
Tomorrow will be my second SCA “event.” I’m going to check out Fool’s War in Macon, GA. Essentially, the Georgia Kingdom and the Florida Kingdom are getting together to beat each other with sticks. I’m not combat trained yet, so I’ll be out there in medieval loaner garb learning more stuff for my endless vault of superfluous minutia. I’ll let you know how it goes.